How to Choose the Right PUR Wrapping Hot Melt Adhesive
Selecting the appropriate PUR (Polyurethane Reactive) wrapping hot melt adhesive is essential for achieving optimal results in your specific application. Given the wide range of formulations available, understanding the key factors influencing adhesive performance will help you make an informed decision. From substrate compatibility to processing conditions, several considerations must be taken into account when choosing the right PUR adhesive for your project.
Substrate Compatibility
The first step in selecting a PUR Wrapping Hot Melt Adhesive is evaluating the substrates involved in your application. Different materials have varying surface energies and textures, which can affect how well the adhesive bonds. For instance, porous materials like uncoated paper absorb more adhesive, while non-porous substrates like plastic or metal require adhesives with higher tack and wetting properties.
If you're working with challenging substrates such as polypropylene or polyester films, opt for PUR adhesives specifically designed for low-energy surfaces. These formulations often include additives that improve adhesion by enhancing the adhesive's ability to spread and penetrate microscopic irregularities on the substrate.
Additionally, consider whether the substrate has any coatings or treatments that might interfere with bonding. Some coatings, such as silicone or wax, can act as release agents, preventing proper adhesion. In such cases, specialized PUR adhesives with enhanced penetration capabilities may be required.
Processing Conditions
Processing parameters, including temperature, open time, and pressure, significantly influence the effectiveness of PUR wrapping adhesives. The operating temperature of the adhesive should align with the equipment capabilities and the thermal sensitivity of the materials being bonded. Most PUR adhesives are applied at temperatures between 100°C and 130°C, but some advanced formulations can be processed at lower temperatures to accommodate heat-sensitive substrates.
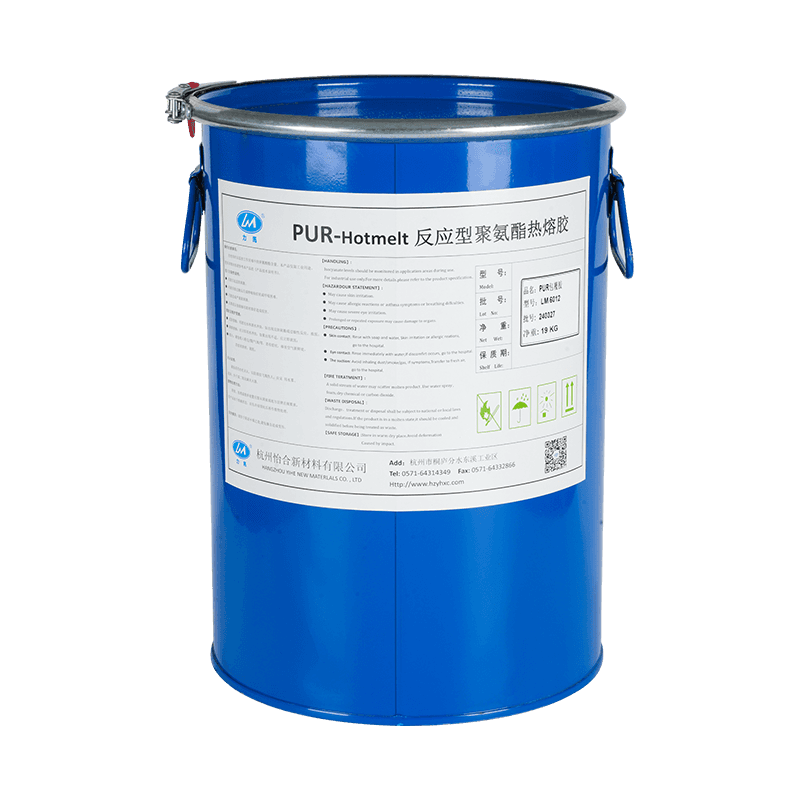
Open time—the period during which the adhesive remains tacky enough to form a bond—is another critical factor. Applications requiring quick assembly, such as high-speed packaging lines, benefit from fast-setting adhesives with shorter open times. Conversely, projects involving complex shapes or larger parts may require adhesives with longer open times to allow for precise positioning.
Pressure is equally important, as insufficient contact between the adhesive and substrate can lead to weak bonds. Ensure that your machinery applies adequate pressure to achieve uniform coverage and eliminate air pockets.
Environmental Resistance
Depending on the end-use environment, the selected PUR adhesive must exhibit sufficient resistance to heat, moisture, chemicals, and UV exposure. For outdoor applications or products exposed to fluctuating temperatures, choose a formulation with high thermal stability and weather resistance. Automotive components, for example, demand adhesives capable of maintaining performance across a wide temperature range (-40°C to +80°C).
Moisture resistance is particularly relevant for packaging applications where the wrapped product may encounter humidity or liquid spills. High-quality PUR adhesives cure to form a waterproof seal, protecting the contents from moisture ingress.
Chemical resistance is also vital for certain industrial applications. If the wrapped item will come into contact with oils, solvents, or cleaning agents, select an adhesive formulated to resist degradation caused by these substances.
Cost vs. Performance Balance
While cost is always a consideration, prioritizing the cheapest option without regard for performance can lead to costly failures down the line. Instead, focus on finding a balance between cost-effectiveness and meeting your application's technical requirements. High-performance PUR adhesives may have a higher upfront cost but can reduce overall expenses by minimizing rework, scrap rates, and downtime.
For large-scale operations, bulk purchasing agreements or custom formulations tailored to your specific needs can further optimize costs. Collaborating closely with adhesive suppliers allows you to access technical expertise and innovative solutions that maximize value.