Future Trends in PUR Wrapping Hot Melt Adhesives
Sustainable Formulations
Sustainability has become a top priority for businesses worldwide, driving innovation in adhesive development. Today's PUR Wrapping Hot Melt Adhesive are being engineered to minimize environmental impact through bio-based raw materials, reduced energy consumption, and recyclable options.
Bio-based PUR adhesives derived from renewable resources like plant oils and starches are gaining traction. These alternatives reduce reliance on fossil fuels and lower carbon footprints without compromising performance. Similarly, waterborne PUR systems are emerging as eco-friendly substitutes for solvent-based adhesives, offering low VOC emissions and improved worker safety.
Recyclability is another area of focus. New formulations enable easier separation of adhesive residues during recycling processes, facilitating the reuse of materials like paper and cardboard. This trend aligns with global efforts to transition toward circular economies, where waste is minimized, and resources are reused efficiently.
Smart Adhesives
The concept of "smart" adhesives—those capable of responding to external stimuli—is transforming the way we think about bonding technologies. Temperature-sensitive PUR adhesives, for example, can activate or deactivate based on predefined thresholds, enabling controlled release mechanisms or self-healing properties. Such innovations hold immense potential for applications in healthcare, electronics, and smart packaging.
Conductive PUR adhesives are also making waves in the electronics industry. These adhesives combine bonding functionality with electrical conductivity, allowing them to serve dual roles in device assembly. As wearable technology and IoT devices proliferate, demand for multifunctional adhesives will likely surge.
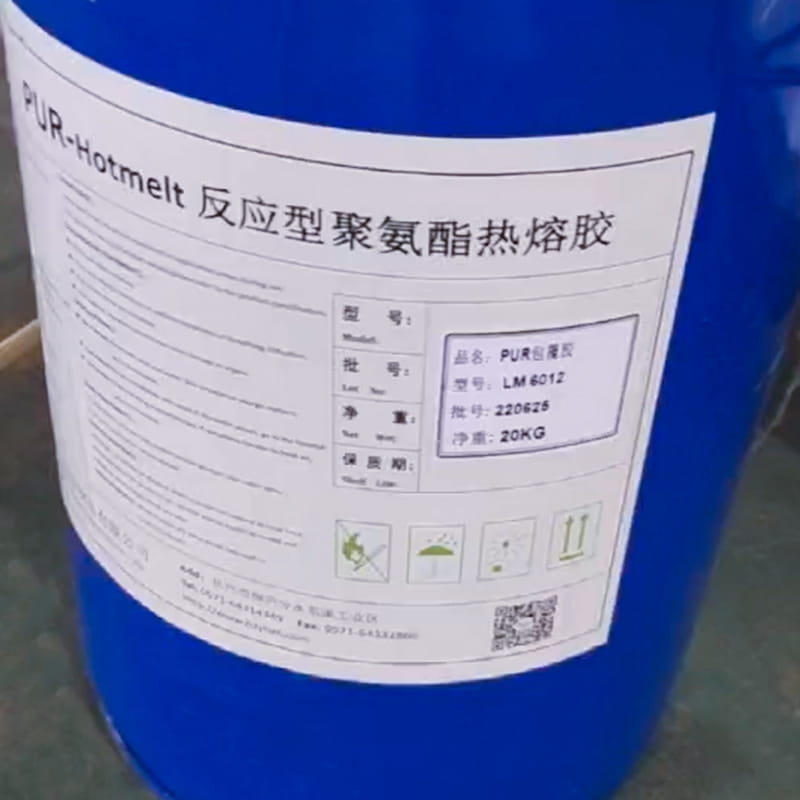
Enhanced Automation Compatibility
With automation playing an ever-larger role in manufacturing, PUR wrapping adhesives are being optimized for seamless integration into automated systems. Low-viscosity formulations and precision applicators ensure consistent dispensing and minimal waste, even at high speeds. This trend supports the growing adoption of Industry 4.0 principles, where real-time monitoring and data analytics enhance operational efficiency.
Adhesive suppliers are collaborating with equipment manufacturers to develop integrated solutions that address specific challenges faced by automated wrapping processes. For instance, robotic arms equipped with PUR dispensing nozzles can achieve intricate patterns and tight tolerances, expanding design possibilities for wrapped products.
Customization and Tailored Solutions
No two applications are identical, prompting adhesive manufacturers to emphasize customization. Advanced R&D capabilities now allow companies to create bespoke formulations tailored to exact specifications. Whether it's adjusting viscosity, curing speed, or adhesion strength, customers can work closely with suppliers to develop adhesives that perfectly match their requirements.
This trend extends beyond technical performance to include branding opportunities. Color-coded or translucent PUR adhesives enable manufacturers to incorporate visual elements into their designs, adding a distinctive touch to wrapped products. Such customization enhances brand recognition and differentiates products in competitive markets.
Expanding Application Areas
As PUR wrapping adhesives become more versatile, new application areas are emerging. Beyond traditional sectors like furniture and automotive, industries such as textiles, medical devices, and aerospace are beginning to adopt these adhesives due to their unique properties.
In textiles, PUR adhesives facilitate the creation of laminated fabrics used in sportswear, upholstery, and protective gear. Their flexibility and breathability make them ideal for garments that require comfort and durability. Meanwhile, in the medical field, PUR adhesives are employed in transdermal patches, wound dressings, and diagnostic devices, thanks to their biocompatibility and gentle bonding characteristics.
Aerospace manufacturers are leveraging PUR adhesives for lightweight composite assemblies, contributing to fuel efficiency and structural integrity. The ability to bond dissimilar materials like carbon fiber and aluminum opens up exciting possibilities for next-generation aircraft designs.