How Does Automotive Interior Adhesive Perform in Extreme Cold Conditions?
Automotive adhesives are essential for ensuring the integrity and durability of vehicle interiors. From securing upholstery to attaching trim, these adhesives must withstand a broad range of environmental factors. Among the most challenging conditions for any adhesive is extreme cold, which can undermine its effectiveness. But how exactly does automotive interior adhesive fare when subjected to freezing temperatures?
The Mechanics of Adhesive Performance in Cold Weather
At its core, adhesive performance hinges on its ability to maintain bond strength across a variety of conditions. Extreme cold affects this performance by altering the physical properties of the adhesive. As temperatures drop, the adhesive becomes less pliable, and the viscosity increases. This means that the bond could become more brittle, leading to a higher likelihood of failure, especially in areas where the adhesive is under strain.
Moreover, extreme cold can cause substrates—such as plastics, metals, or fabrics—to contract, which may lead to a mismatch between the adhesive's bonding properties and the surface it is intended to secure. A poorly matched adhesive can result in peeling, delamination, or even complete detachment.
Types of Automotive Adhesives and Their Cold-Weather Durability
Not all adhesives are created equal, especially when it comes to temperature resilience. Some are specifically formulated to withstand extreme cold without compromising their effectiveness.
Epoxy Resins: Epoxy adhesives are generally recognized for their superior bonding strength and resistance to temperature fluctuations. Many modern formulations have been engineered to endure harsh winter conditions without losing their adhesive properties. They maintain high tensile strength, even in freezing temperatures, making them a preferred choice for many high-performance automotive applications.
Polyurethane Adhesives: These adhesives offer a degree of flexibility that can be advantageous in cold conditions. While they may not have the sheer strength of epoxy, polyurethane adhesives retain their flexibility in freezing temperatures, preventing cracking and maintaining strong adhesion.
Silicone-Based Adhesives: Silicone adhesives, often used for sealing and bonding, are highly resistant to temperature extremes. They maintain excellent adhesion even in temperatures well below freezing, owing to their inherent flexibility and strong bond capabilities.
However, despite these advancements in adhesive technology, automotive manufacturers must take great care to choose the correct adhesive for each application. Factors such as the type of material being bonded, the location within the vehicle, and the severity of the cold conditions all play pivotal roles in determining whether a particular adhesive will perform optimally.
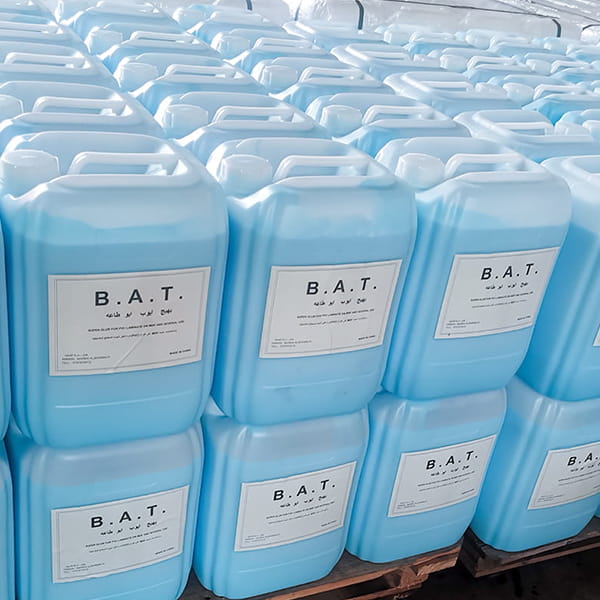
Challenges of Cold-Weather Performance
Extreme cold can introduce several challenges that can compromise adhesive integrity. These include:
Increased Rigidity: Cold temperatures can cause adhesives to become too rigid, weakening the bond between materials. In some cases, the adhesive may even crack, leading to complete failure of the bond.
Slower Cure Times: Many adhesives require specific curing times at certain temperatures to achieve their maximum strength. In extremely cold conditions, cure times may be extended, delaying the bonding process and compromising initial adhesion.
Environmental Factors: In addition to temperature, the presence of moisture, snow, or ice can negatively impact adhesive bonds. Cold conditions often coincide with higher humidity levels or direct exposure to wet elements, which can interfere with adhesion and promote corrosion or degradation of the adhesive material.
Testing and Innovation in Cold-Weather Adhesive Performance
To combat these challenges, automotive manufacturers and adhesive companies have invested heavily in research and development. Rigorous testing ensures that adhesives meet strict standards for cold-weather performance, simulating real-world conditions like freezing temperatures and moisture exposure. This testing has led to innovations such as the creation of hybrid adhesives that combine the best qualities of multiple materials, offering improved performance in extreme conditions.
Further advancements include the development of adhesives that are reactive to temperature changes, allowing them to adjust their properties as conditions shift. Such technologies are already being tested in the automotive industry and are expected to play a significant role in improving vehicle interior durability.
The Future of Automotive Adhesives in Extreme Cold
Automotive interior adhesives, while sensitive to extreme cold, continue to evolve and improve. With advancements in adhesive technology, modern formulations are becoming increasingly reliable in maintaining strong, durable bonds under freezing conditions. Whether through increased flexibility, faster cure times, or the ability to withstand moisture and temperature fluctuations, these innovations ensure that automotive adhesives are ready to meet the demands of cold-weather performance.
In the near future, we can expect even more robust solutions, offering greater reliability and longer-lasting bonds—critical to enhancing vehicle quality and longevity in challenging environments.